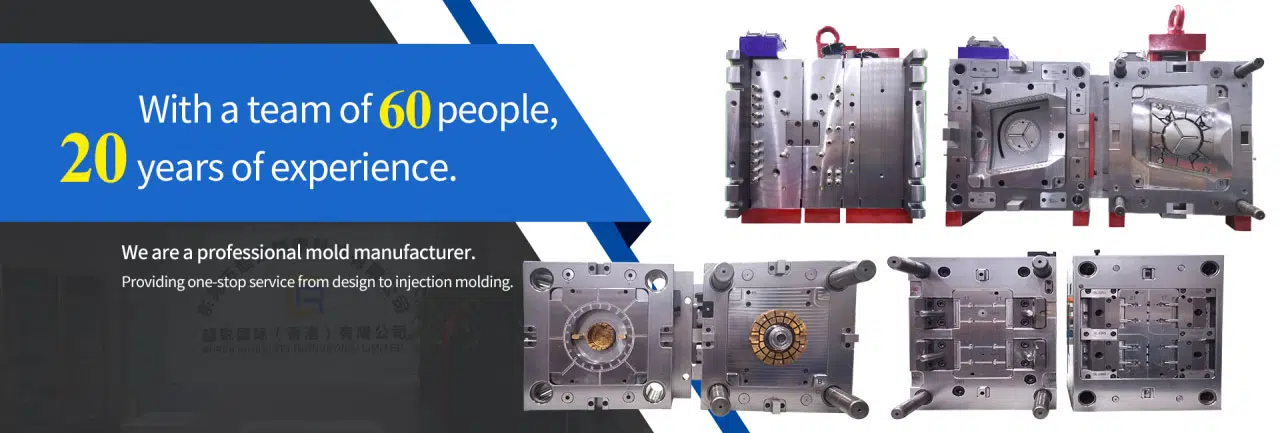
。
# Anodizing Process and Applications in Modern Industry
## Introduction to Anodizing
Anodizing is an electrochemical process that converts the metal surface into a durable, corrosion-resistant, anodic oxide finish. This process is most commonly applied to aluminum, but can also be used for other metals such as titanium and magnesium. The anodized layer is integral to the metal substrate, making it highly resistant to peeling and chipping.
## The Anodizing Process
The anodizing process involves several key steps that transform the metal surface:
### 1. Cleaning
The aluminum part is thoroughly cleaned to remove any dirt, grease, or other contaminants that might interfere with the anodizing process.
### 2. Etching
The part is then etched in a chemical solution to remove a thin layer of aluminum, creating a uniform surface texture.
### 3. Anodizing
The cleaned and etched part is submerged in an electrolytic solution (typically sulfuric acid) and an electric current is applied. This causes oxygen ions to be released from the electrolyte and combine with aluminum atoms at the surface, forming aluminum oxide.
### 4. Coloring (Optional)
After anodizing, the porous oxide layer can be dyed in various colors before sealing. This is achieved by immersing the part in a dye bath.
### 5. Sealing
Keyword: Anodizing
The final step involves sealing the porous oxide layer to enhance corrosion resistance and durability. This is typically done by immersing the part in hot water or steam.
## Types of Anodizing
There are several types of anodizing processes, each with specific characteristics:
### Sulfuric Acid Anodizing
The most common type, producing coatings from 0.0001 to 0.001 inches thick. It offers good corrosion resistance and is suitable for coloring.
### Hard Anodizing
Produces thicker, harder coatings (0.001 to 0.003 inches) with excellent wear resistance, often used for industrial applications.
### Chromic Acid Anodizing
Creates thinner coatings with good corrosion resistance, often used in aerospace applications where fatigue resistance is critical.
## Applications in Modern Industry
Anodized aluminum finds applications across numerous industries due to its exceptional properties:
### Aerospace Industry
Anodized components are widely used in aircraft due to their corrosion resistance, durability, and ability to withstand harsh environmental conditions.
### Automotive Industry
Many automotive parts are anodized for both functional and aesthetic purposes, including trim pieces, wheels, and engine components.
### Architecture and Construction
Anodized aluminum is popular for building facades, window frames, and curtain walls due to its weather resistance and aesthetic appeal.
### Consumer Electronics
Many electronic devices use anodized aluminum for casings and components, benefiting from its durability, lightweight properties, and modern appearance.
### Medical Equipment
Anodized aluminum is used in medical devices and equipment where corrosion resistance and cleanliness are essential.
## Advantages of Anodizing
The anodizing process offers numerous benefits that make it valuable in industrial applications:
– Enhanced corrosion resistance
– Increased surface hardness and durability
– Improved adhesion for paints and adhesives
– Excellent wear resistance
– Aesthetic versatility with color options
– Environmentally friendly compared to other coating processes
– Non-conductive surface (after treatment)
– Maintains metallic appearance while providing protection
## Conclusion
The anodizing process continues to be a vital surface treatment in modern industry, offering an optimal combination of protection, durability, and aesthetics. As technology advances, new applications for anodized metals continue to emerge across various sectors. Its environmental benefits and superior performance characteristics ensure that anodizing will remain a preferred surface treatment method for aluminum and other metals in the foreseeable future.