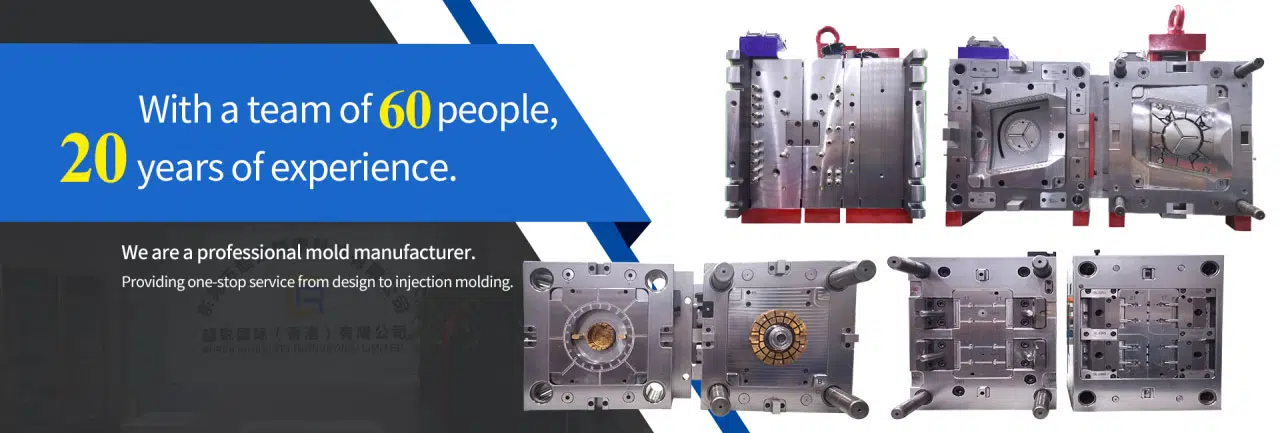
# Die Casting Process Optimization for High-Quality Aluminum Components
## Introduction to Die Casting
Die casting is a highly efficient manufacturing process that produces precise, complex, and durable metal parts. Among various materials used in die casting, aluminum stands out due to its excellent properties, including lightweight, high strength-to-weight ratio, and corrosion resistance. The die casting process involves forcing molten metal under high pressure into a steel mold (called a die), where it solidifies into the desired shape.
## Key Factors in Die Casting Optimization
To achieve high-quality aluminum components through die casting, several critical factors must be optimized:
### 1. Mold Design and Maintenance
The die design significantly impacts the final product quality. Proper gating systems, venting, and cooling channels must be incorporated to ensure smooth metal flow and minimize defects. Regular mold maintenance prevents wear and tear that could affect dimensional accuracy.
### 2. Process Parameters Control
Precise control of process parameters is essential for consistent quality:
– Injection pressure and speed
– Metal temperature
– Die temperature
– Cooling time
– Ejection mechanism
### 3. Material Selection and Preparation
Choosing the right aluminum alloy for the application is crucial. The molten metal must be properly prepared with:
– Correct alloy composition
– Proper degassing to remove impurities
– Consistent temperature control
## Advanced Techniques for Quality Improvement
Modern die casting facilities employ several advanced techniques to enhance quality:
### 1. Vacuum-Assisted Die Casting
This technique removes air from the die cavity before injection, reducing porosity and improving mechanical properties.
### 2. Squeeze Casting
Combining die casting and forging principles to produce components with superior mechanical properties and reduced porosity.
### 3. Real-Time Monitoring Systems
Keyword: Die Casting
Advanced sensors and control systems monitor process parameters in real-time, allowing for immediate adjustments to maintain quality standards.
## Quality Control Measures
Implementing robust quality control measures ensures consistent production of high-quality aluminum components:
– Dimensional inspection using CMM (Coordinate Measuring Machines)
– X-ray inspection for internal defects
– Mechanical property testing
– Surface finish evaluation
– Leak testing for pressure-tight components
## Benefits of Optimized Die Casting
A well-optimized die casting process offers numerous advantages:
– High production rates with excellent repeatability
– Tight tolerances and excellent surface finishes
– Reduced material waste compared to other manufacturing methods
– Ability to produce complex geometries with thin walls
– Cost-effectiveness for high-volume production
## Conclusion
Optimizing the die casting process for aluminum components requires attention to every detail, from mold design to final quality inspection. By implementing proper process controls, advanced techniques, and rigorous quality measures, manufacturers can consistently produce high-quality aluminum parts that meet the most demanding specifications. As technology advances, die casting continues to evolve, offering even greater possibilities for producing superior aluminum components across various industries.